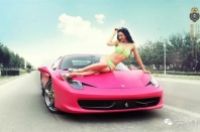
试制在汽车研发中的地位不言而喻,不可缺少,就像生活中,要有美,如果总是苦难,生活将枯燥乏味,对未来失去信心,然而有了美,就会对未来充满期待,也会增加很多乐趣,比如看看下面这个美女,就会让人善心悦目,这也是生活中的一种美!
一
试制验证概念
试制是按照设计要求将设计方案由图纸转换为实车的过程,验证设计的正确性、符合性,并暴露存在可装性、符合性等各类问题和结构、整车匹配的优化性建议,反馈设计进行修改后的实物再次验证,直至闭环为止,确保向生产线输出正确的图纸。
可分为如下两类:
1、样品试制
根据设计图纸,工艺文件和少数必不可少的工艺装备,由试制车间试制出一、二件产品,以便检验产品的结构、性能及主要工艺是否达到设计要求,设计图纸是否正确,以便肯定或进一步校正产品设计。
2、小批量试制
通过鉴定和校正修改后,根据成批生产和大量生产的要求,编制全部工艺规程,设计制造全部工艺装备,然后生产一小批产品。目的是检验工艺规程和工艺装备是否适应生产的要求,并对产品图纸进行工艺性审查,以便进行必要的校正,为大批量生产创造条件。
二
试制验证目的
对于汽车研发而言,试制的目的就是提升设计图纸的准确率,降低新产品批量上线问题数和产品成本,为设计做好验证服务工作。
三
整车试制验证核心流程
四
试制验证流程的意义
建立科学合理的整车试制验证流程对于新产品开发和试制验证工作开展具有重要的实用价值和意义。充分发挥产品试制过程中涉及部门的各自优势及特性,合理优化资源,简化交接流程,严控必要质量把关环节,从而提高了整车试制的质量和管理水平,在缩短整车试制周期、降低试制成本、改善试制产品质量、提高试制效率等方面起到至关重要的作用。
五
关键过程识别
项目立项后项目经理、试制人员和设计人员需联合确定项目全生命周期过程的《车辆规划表》,如下:
2、试制周期核定
整车试制计划周期确定依据试制流程,恪守关键节点,根据试制现有资源条件各车型实际按照流程运行时经历的工时决定。
以某4系多功能商用车为例,据车型试制特点此类整车的试制验证的工时为80小时/台,包含试制装配人员到试制库房领料和试制过程问题反馈时间,此类整车试制周期为10个工作日。
某4系多功能商用车试制周期核定依据
3、试制计划制定与发布
试制模块组长每月按试制节拍完成编制并发布《试制月度计划》,每周末完成编制并发布《试制周计划》,具体装调验证班组依据上述计划分解成自身日计划。
4、试制任务的下发与接收
总布置负责人下发《产品试制项目任务单》,任务单内容包含车辆主要配置,参数,车辆用途和车辆试制起止时间等信息,《产品试制项目任务单》必须有总布置负责人,项目经理和项目总监签字有效,接收人为试制模块组长。
5、技术文件的下发与分解
项目组各分组需向试制部下发的支撑文件有:
6、试制物料筹备与管理
1)专用件管理
各分组把专用件采购单下发协同开发后。协同开发编制基础监控表发给试制,包含厂家信息、预计到货时间、台套数量等基础信息,试制转化为《项目物料监控表》,项目组内部发布。
A、入库:协同开发同供应商下发采购计划单的同时下发ERP采购订单,厂家送货时自带送货清单、协同下发的采购计划单及产品自检报告,库管员确认零部件实物图号、ERP订单图号与监控表图号一致后收货并出具ERP入库验单。检测不合格件厂家重做重新配送,直到合格,库房不重复出具入库验单。
B、出库:检测合格后,件入库房保管,根据装车进度发放,并出具ERP系统拣货单,领料人及其直属领导签字确认。加急件可以不入库房,检测后直接装车,但必须至库管员处补办出库手续。
C、送检:专用件监控表整理好后直接发给质量管理检测室识别可检件,到货后库管员根据检测室识别结果开具送检单将零部件附带厂家检测报告送检。
2)借用件管理
整车BOM下发后,分解成调拨件(试制领用件)、直送工位件、标准件。
A、调拨件(试制领用件):分解、查询制造公司库存情况,领料员出具单据至各个专业厂库管员处调拨领料;调拨完成后交各库管员入库保管、库管员出具入库验单,同时更新物料监控表到货情况(每日反馈到货情况);
B、直送工位件:协同开发负责采购并跟踪到货情况,库管员负责收货、按项目按车型入库房管控,出具入库验单,同时更新物料监控表到货情况(每日反馈到货情况);
C、标准件:标准件为车间常备件,无特别要求视同车间有库存,物料根据装配人员反馈定期补缺。
7、整车装配、调试与验证
装调班组依据技术组提供的技术工艺文件对整车进行装配、调试验证。
1)车辆油水加注
车辆装配完成后车辆装配负责人对整车进行调试准备,首先按照下表顺序加注各项油水,各类油液加注型号需各设计分组提供给试制装配负责人,如下表。
2)车辆电气功能调试
车辆油水加注完毕后进行电气功能调试,调试顺序如下:
3)车辆行驶功能调试
车辆班组评审及整改完成后转移给试制质量控制室进行整车AUDIT评审和主观动态评价,原则上每批次Mule Car,P0车和量产车均需组织静态评审和动态主观评价,质量室将评审/评价的问题反馈至试制组长处,统一反馈项目组,纳入监控管理。
9、试制过程问题反馈
根据项目运行流程及项目中质量管理实际运行特点,项目试制问题以《试制问题监控表》的形式进行反馈;车辆开始试制验证日起装配人员将车辆现场装配过程发现的问题反馈给试制组长,试制组长反馈给质量管理项目负责人,由质量管理负责人统一在全项目组内管控;各分组接收到试制问题反馈后按照质量管理部要求在规定日期内对问题进行回复,问题闭环需打《试制问题闭环报告》,由问题提出方,质量人员和设计员三方现场确认后问题闭环,如下表:
通常车辆完成时,会提交车辆完工确认表,以表示车子已经按照项目需求完成试制,并且已满足车辆试验需求,需要各专业人员签字确认,最后由试验人员接车,开始做试验。
1)车辆过程管理
C、试制物料管理室负责对车辆借用,钥匙登记,车辆归还及验车的实际管理工作,试制技术工艺负责人负责项目车辆具体状态管控,定期发布项目车辆管控表至项目组,如下图:
2)车辆处理
A、入库:试制工艺员与项目经理对接梳理完成利用需要入库的车辆后,车辆使用人必须第一时间停止所有试验和改制,车辆归还交付试制部验收,并按入库要求进行整改,完毕后交付物料室办理入库手续;
B、报废:试制工艺员与项目经理对接确认车辆利用完毕且不具备入库销售条件的车辆走车辆报废流程,试制工艺员将报废处理车辆信息下发试制物料室同时在项目组内部公示,试制物料室走报废销帐流程。
六
结论
通过对整车试制流程的梳理和试制过程关键路径的识别,和大家聊清楚了整车试制验证目标和管理机制,理清了流程,使得过程作业有效化和标准化,对在整车试制验证中各环节出现的问题,都有明确的反馈处理流程和目标责任人,使得试制验证的有效性得到了很好的强化。
整车试制验证是一个非常复杂的系统工程,可能用到的过程管理方法也很多,本文所述的某一种试制验证流程不一定适合每个企业,企业需根据自身条件和新产品的特点同时考虑投入成本、开发周期与质量要求,建立适合自己的试制验证流程。