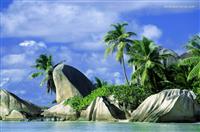
摘要:目前,在生产球墨铸铁件的企业中,广泛采用稀土镁硅铁合金作为球化剂。现在普及使用电炉熔炼的企业中,通常使用5-8或3-8稀土镁硅铁合金。因电炉熔炼的铁水硫含量不高,大部分企业使用3-8稀土镁硅铁合金。虽然部分企业已在使用喂丝球化孕育处理工艺,但仍有企业还在使用传统的冲入法球化处理工艺。所以有必要把本人在球化处理(冲入法)实际操作的心得体会分享给大家,望对大家在生产中有所帮助。
关键词:球化包 球化处理 浇注时间 质量控制 质量检验
一.球化包
1. 球化包是重要的球化处理工具。球化包除具有一般铁液浇包所具有的操作方便,手轮转动灵活,自锁性好,安全可靠外,还应有利于球化反应过程中球化元素的吸收。一般高径比(H/D>1.5-1.8)即细高型。球化元素在铁水包中吸收的路径加长,有利于充分吸收。
2.砌筑。在球化包底及四周砌筑耐火砖,注意把砖缝挤紧。在包底砌筑堤坝,用大砖(整块)或耐火砖立砌,注意挤紧压实。堤坝应与包嘴有30º夹角,有利于把球化包内的剩余铁水全部倾倒完。
3.搪包衬。先用面砂对包底填砂,用平锤平整捣实,既夯实包底又加固堤坝。堤坝高度以盛装好球化剂、孕育剂、铁屑后高出40-80mm。搪包材料用造型面砂和耐火土按4:1搅拌均匀,干湿程度比面砂稍微偏湿。装入包内,由上到下用手搪于包的四周,要求厚度均匀,用胶皮管用力敲打,压平压光。
4.烘烤。要求必须烘干烘透! 否则球化包包衬中的水分与镁元素发生化学反应,产生沸腾现象,容易导致整包铁水报废。
5. 修补。烘干后需对裂纹进行修补,修补后用黑芡粉涂料对内壁涂刷,防铁水粘包。在使用过程中,应随时检查包衬耐火材料是否脱落,发现脱落要及时修补。
二.球化处理
1. 装料。严格按照球化孕育处理工艺要求操作。已知铁水量,使用电子秤称取球化剂和孕育剂。先将球化剂、孕育剂和铁屑依次放入球化包的反应堤坝内,并依次用捣锤平整捣实。捣实程度依据球化反应的强弱程度进行调整,然后再用聚渣剂平铺一层。所有的一切均为了延缓球化剂的起爆时间,从而提高吸收率。
2. 球化反应。当铁水的化学成分和温度均符合工艺要求时,开始出铁球化处理。
(1)注意调整好球化包的停放位置,必须保证铁水的冲入位置是放球化剂及孕育剂的另一侧堤坝内,切忌直冲球化剂。否则严重影响球化剂的吸收。
(2)开始出铁时流速要快易于起爆,待反应激烈时,逐渐减小流速不断流。随着球化反应的由强变弱逐渐加大流速,理想状态为:铁水放至要求值时,球化反应刚好停止。需要掌握球化反应和出铁流速的合理搭配。
(3)拔渣处理:反应结束后,用聚渣剂撒入铁液表面搅拌,拔渣处理2-3次,将渣拔净后,再用聚渣剂覆盖严实铁液表面。加入量为拔渣时的2倍。
(4)浇注。在倒包过程中,聚渣剂要时刻浮在铁液表面,不得挂在包壁上,防止球化元素的逃逸,同时对铁液起保温作用。
三.浇注时间:球化反应结束至浇注完最后一型的时间。铁液原则上必须在8分钟之内浇完。理想的浇注人数:小件(端包)3-4人/组,大件(抬包)6人/组。
四.质量控制
1. 球化温度要适宜。理想温度为1480-1520ºC。
(1)温度偏高,球化反应时间短,球化元素烧损大,造成球化衰退或球化不良。措施:出铁时视情况添加冷铁降温。
(2)温度偏低,球化反应时间长,甚至在出完铁水还反应。将造成铁水温度低,流动性变差,铸件易出现气孔或冷隔等缺陷。措施:出铁20秒后还没有起爆,应直接用铁水冲击球化堤坝引爆反应。球化反应时间在60-90秒之间。
2. 球化剂加入量要适宜。根据出铁温度,出铁量,铸件形状大小和壁厚,浇注时间长短来确定加入量。
(1)加入量偏大,则铁水中的含镁量和稀土量升高,降低了机械性能。造成石墨球异化,反白口,加大缩孔缩松倾向,黑渣等缺陷。
(2)加入量偏小,则铁水中的含镁量和稀土量降低,造成球化不良或球化衰退等缺陷。
3.出铁量。必须听从配料员的指令,因为球化剂加入量是按出铁量确定的。铁水多出,则铁水中的含镁量降低,可能造成球化衰退和球化不良。铁水少出,则铁水中的含镁量和稀土量升高,降低了机械性能。
4.浇注时间。应严格按照工艺要求执行。
结论:出铁温度,球化剂加入量,出铁量和浇注时间必须严格按照工艺要求来执行,产品质量才能保证!
五. 质量检验。对每包球化铁水在浇注完最后一型铸件时,需对该型插棒标识,同时浇注金相试块,用于检验本包铁水的球化情况。若球化级别为2-3级视为合格。若大于等于4级视为球化衰退,须对本包所浇注的铸件进行隔离标识。待正常冷却后,对铸件断口逐件检验分拣,不合格品报废回炉使用。