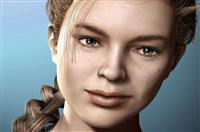
利润薄如纸!
卖得多,赔得多,不卖或是少卖,又惧怕失掉市场。
当前形势下,正有越来越多的中国制造业企业面临着以上困局,以至于有人慨叹,“上帝若要惩罚谁,就让他去做制造业好了。”
但是,近80年来,日本这家制造业企业却凭着极致的精益管理,从偏安于一隅的小企业,跃升为全球汽车产业巨头,并造就了“有路必有丰田车”的神话。2016年,更是凭着1017.5万辆的销售业绩,连续第二年全球销量突破千万辆大关。
这家企业经营的秘诀究竟是什么?有人用一句话这样概括:最会过日子的家族找了几个更会过日子的管家过出了变态极致的运营。
虽说有些夸张,但也是很精准。
“针上打擂,拼精细。”认真做好每个细节,伟大就能不期而至。这里有7条精华,供你参阅。
只生产足够:艺术大师总是善于在限制中表达
大野耐一,丰田生产方式(TPS)创始人,被誉为“日本复活之父”、“生产管理的教父”、“穿着工装的圣贤”,其精益管理法受美国超市的启发而诞生。
大野指出,客人只买必要的商品,店员业只补充能卖掉得那部分。这样一来,就不需要多余的存货,也不会浪费钱。多余的东西只会白白占用资金。
他一改前人的做法,要生产的产品只要刚好够就好,“不生产多余的产品”,“不要有库”。必要的产品,只在必要的时间,生产必要的数量,做得太多就是浪费。
事实上,艺术大师总是善于在限制中表达自己(歌德语)。丰田管理的几位先驱,实为不折不扣的“艺术大师”,他们能使生产过程的浪费与成本最小化,并通过可持续的过程改善,真正做到了“拧干了毛巾里的最后一滴水。”
控制人心:不把员工当猪看
第一线工作者,是最了解问题的专家,大野耐一称,“没有人喜欢自己只是螺丝钉,工作一成不变,只是听命行事,不知道为何而忙,丰田做的事很简单,就是真正给员工思考的空间,引导出他们的智慧。”
在丰田,小到如何省下一个螺丝钉,都可以被奖励。以丰田设在台湾的国瑞厂为例,平均每月有3500件提案,每个员工至少提案1.2个,采用率达8成以上,改善提案规划14个层级发放奖金。
钱,并非不是丰田改善的主要诱因,奖金金额不高,有时只有几百元而已,但是大家会有成就感,因为被公开奖励。自己提出的方案被标准化,落实在生活四周,会觉得自己创造了很多过去没有的价值,把改善变成了习惯。
匠心:人,永是产品的最后一关
一生只做一件事,穷尽一生磨练一个技能。练物即练心,匠心,可谓是日本人终生的信仰。
那么,丰田的工匠是怎么产生的?这里举个例子。
丰田北九州工厂的培训室有三个考核项目非常有趣,据说每周厂里都会有类似的实际操作考试,以评定一线工人的制造水平到底是在进步还是在退步。
测试A:左手单手(左撇子相反)在一分钟之内折出一只小猫脸;
测试B:将按照直径大小排列的30个圆柱形积木块快速码放进对应的孔状模具中(随机排列);
测试C:在一块长方形的白色壁板上用喷漆罐喷出均匀且尽量笔直的横线。
其中,项目A和B同时考察时间和准确度,项目C以考察准确度为主。看似简单的测试到了菜鸟手里,其结果会惨不忍睹。难怪在丰田的总装线上,每一道零件组装工序的时间都被精确到几秒,甚至零点几秒。
工匠其实也是练出来的,“如同玩家手中的游戏机,闭着眼都能摸着操作。”一位丰田技师讲,熟悉是能工巧匠的必由之路。
人工操作是为了让人能够掌握的工序更加精益求精,虽说现在有可替代的机器人,但在丰田,人,永远是产品的最后一关。
揪出魔鬼:要问五次为什么
必须把流程中的魔鬼挑出来,这在丰田,是一种精神,不只是管理工具。
例如当机械停止工作时,就要展开如下工作:
为什么机械会停止工作?
因为机械过载,保险丝烧了。
为什么机械会过载?
因为轴承部分没有被充分润滑。
为什么轴承部分没有被充分润滑?
润滑油泵没有吸上来足够的润滑油。
为什么没有吸上来足够的润滑油?
因为润滑油泵的轴承有了损耗,轴承摇摇晃晃。
为什么有损耗?
因为没有安装过滤器,进入了粉尘所致的。
这就是丰田著名的“五W”原则:反复问Why(为什么)、Why(为什么)、Why(为什么)、Why(为什么)、Why(为什么),直到发现Why(为什么)。
丰田生产方式的改善就是追究到问题的真正原因。如果没有寻找到真正原因,不仅相同的问题以后还会重复出现,甚至还会产生更大的问题。
追求极致:最可怕的力量
《哈佛商业评论》曾称:“丰田最可怕的,是一种原则的力量,一种追求极致的思维,而不是生产工具与方法而已。”
让我们来看看下面一组数字,你就能感受到:
在台湾,电子业的不良率在千分之五到千分之十;在丰田,这数字的境界是:百万分之七。
在组件方面,汽车有30000个零件,而信用卡公司处理的消费者申请数据只有50项;在往来对象的复杂度上,车厂必须与450家企业往来零件,而信用卡公司的上下游往来只有两端(消费者、银行)。虽然面对更复杂的组件与往来对象,但丰田制造一部车需要不到100个员工,但是信用卡却需要150个人;在时间上,丰田10小时能做好一辆车,但信用卡发卡却需要4到6天。
也就是说,所有的细节都被精密计算。以铁锤敲钉子举例,对丰田而言,伸手去拿铁锤就是没有意义的,必须尽量把时间缩短甚至消除,因为,唯有拿铁锤敲下钉子的那瞬间,才有价值。
年轮经营:每个人心里一个梦,种桃种李种春风
从2012年到2015年,丰田汽车一直是全球销量霸主,而在过去的2016年,“霸主”成绩虽未能延续,但其依旧凭着1017.5万辆的销售业绩,连续第二年全球销量突破千万辆大关。
不过,如今,“数字”增长已不再是丰田发展的核心。社长丰田章男早在2014年就开始推行“年轮经营”的理念,鼓励丰田人要正确处理好企业发展速度和经营质量的关系,不断稳固基础,立足长远发展,注重环境和谐,像“年轮”一样扎实成长,企业才能经历风雨,保持健康发展。
所谓“每个人心里一个梦,种桃种李种春风”。年轮越密,基础越牢固。
丰田章男强调称,他不会去追求数字,因为数字会让人跑偏。“我们制造汽车的出发点是什么?是要让人享受汽车带来的愉悦,带来幸福指数的提高。‘超越你的期待’是丰田一直追求的目标。”
简单思考,认真执行
简单是高级形式的复杂,丰田做到了这一点。外在形式越简单的东西,智慧含量就越高,因为它已经不在依赖形式,而依靠智慧。
比如,丰田精益模式,表面上看非常简单,但真正能学到手,并运用出成效的,就全世界范围内也是凤毛麟角。因为这里面,有组织架构、流程体系,物流与转换体系,绩效与文化保障体系等诸多的不兼容等等。
再比如,丰田坚持简单的内部沟通,但它的社会网络基础复杂。一条不成文的规则是:丰田的员工互相沟通时必须保持简单的语言。在做总结汇报的时候,他们必须单页纸内总结背景资料、目标、分析、行动计划和预期的结果。
与此同时,丰田助长了复杂的社会网络,因为它要“每个人都知道一切。”
原标题:《利润薄如纸,制造业该怎么活?这家日企给出了极致“变态”运营法》